Operational efficiency is a measure of how effectively a company can deliver high-quality products or services while minimizing costs. This concept is crucial for both large corporations and small businesses. By focusing on streamlining processes and reducing waste, businesses can significantly enhance their productivity and competitiveness.
Improving operational efficiency involves refining workflows, implementing data-driven decision-making, and utilizing resources smartly. It impacts various aspects of a business, from customer satisfaction to financial performance. This article discusses the impact of operational efficiency, differentiates it from effectiveness, explores lean principles and offers strategies for measuring and improving operational efficiency.
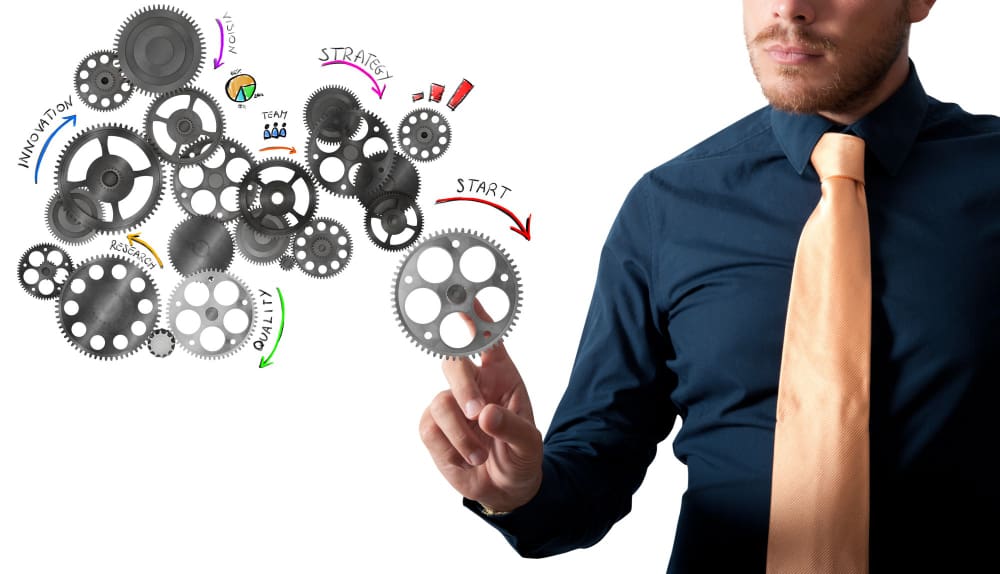
How Operational Efficiency Impacts Businesses
Operational efficiency reshapes how businesses handle costs, productivity, and expansion. By adopting streamlined processes and minimizing waste, companies can decrease expenses and boost profits. These savings enable investment in new opportunities or can be transferred to customers as cost savings.
Efficiency allows companies to complete tasks swiftly with fewer resources, enabling teams to concentrate on essential projects rather than repetitive duties. In competitive markets, efficient businesses attract customers through better pricing, faster services, and superior-quality products.
Efficient operations also facilitate easier scaling and adaptation to market changes, such as launching new products or entering fresh markets. Fewer delays and problems contribute to improved customer satisfaction, which fosters repeat business and positive recommendations.
Operational Efficiency vs. Effectiveness
Though often used interchangeably, operational efficiency and effectiveness refer to different business facets. Efficiency focuses on cost-effectiveness by minimizing waste and refining processes, while effectiveness is about achieving desired results and aligning processes with business goals. Both are necessary for success.
Efficiency covers aspects like speed, cost control, and resource maximization. For instance, enhancing a manufacturing process to produce more units per hour with fewer resources exemplifies efficiency. It concerns how well tasks are executed.
Effectiveness pertains to outcomes and their significance for the business. For example, producing high-quality products while meeting customer needs signals effectiveness, even at a higher cost. Both efficiency and effectiveness are vital for businesses aiming for success.
Lean Principles and Their Role in Efficiency
Lean principles help businesses accomplish more with fewer resources by eliminating waste. Originally developed for the automotive industry, these principles streamline processes, improve quality, and raise productivity.
The core lean principles include identifying customer value, creating a value stream map, ensuring continuous flow, implementing a pull system, and striving for perfection. These principles focus on eliminating non-value-adding activities to save time and money.
A value stream map visually outlines each step of product or service delivery, identifying redundant steps and bottlenecks for improvement. A pull system driven by customer demand avoids overproduction and lowers storage costs.
Lean principles also emphasize ongoing improvement and innovation by relentlessly refining processes to eliminate waste. This constant development keeps companies competitive and efficient.
Measuring Operational Efficiency
Evaluating a company’s use of resources in producing goods or services involves various metrics. Monitoring these metrics helps businesses identify areas for improvement and make informed decisions.
The cost-to-revenue ratio compares total operating expenses to revenue, with a lower ratio indicating higher efficiency. Another metric is productivity, measuring output against input, like revenue per employee or units produced per machine hour.
Cycle time evaluates the total time required to complete processes, highlighting areas for efficiency gains. Likewise, capacity use rate measures the percentage of potential output used in production.
Waste reduction is essential for efficient resource use, with lean techniques like Six Sigma minimizing waste. Inventory turnover gauges how frequently inventory is sold and replaced, reflecting management efficiency.
First pass yield (FPY) measures the proportion of defect-free products produced initially, indicating efficient processes. A high FPY reduces reworking costs and enhances resource utilization.
Improving Operational Efficiency
To maximize resources while maintaining product quality, companies can adopt various strategies. Mapping out current processes helps visualize work flows and identify inefficiencies or redundancies.
Eliminating waste involves identifying and addressing resource wastage areas, such as overproduction, long wait times, and repetitive tasks. Lean tactics or Six Sigma methods can systematically reduce these areas.
Automation is a powerful tool for managing repetitive or time-consuming tasks, increasing reliability and freeing up team members for more creative efforts. Employee training and engagement are also crucial for maintaining skills and motivation.
Setting performance goals with aligned metrics, like process completion times or inventory turnover rates, enables data-driven decisions. Real-time inventory management tools assist in maintaining optimal stock levels while just-in-time (JIT) techniques reduce inventory costs.
Streamlined communication ensures effective information sharing and collaboration. Utilizing project management software and feedback loops keeps teams aligned, allowing swift decision-making and issue-resolution.
Operational efficiency is indispensable for businesses aiming to maximize output while minimizing input. Integrating efficient practices enhances quality, speeds up delivery, and reduces costs, ultimately building a stronger business model.